Butt Splices, Step-Downs, and Wire Joints
Posted by Pacer on 10th Jul 2023
A look at what separates these connectors, the similarities they share, and where you want to use them.
What do Butt Splices, Step-downs, and Wire Joints have in common?
Rather than diving straight into what differentiates these connectors, let’s start by covering what factors they share. All three of these types of connectors are used to connect wires together or to terminate a wire at an endpoint. That is to say that they are all electrical connectors used to complete a circuit or create a dead end. They are also made of tinned copper and are available in various insulation types. This means that these connectors are all designed to withstand corrosion and exposure to the elements making them perfectly suited for use in the marine environment. Now that we know the similarities they share let’s turn our attention to the differences between them.
"Designed to withstand corrosion and exposure to the elements making them perfect for use in the marine environment."
What differentiates these connectors from one another?
The main difference between these connectors is the applications where they are used. Butt splices are used in applications where a wire needs to be connected to another wire of approximately the same size. This could be something as simple as connecting wires on a panel or similar piece of equipment or to repair damaged wire. Butt splices work on the same principle as a bridge where the splice acts as a connection point between two wires.

A step-down is a specified version of a butt splice that is designed when one or more wires of various sizes need to be connected to one or more additional wires. For example, a step down may be used when one side of a connection has three 12 AWG wires that need to be connected to four 14 AWG wires. In this way, step-downs allow you to take a given wire and “step-down” by connecting it to another, different sized wire.
Wire joints are like butt splices and step downs only wire joints have a single opening whereas butt splices and step downs always have two. A wire joint can be used in the same as butt splices. Often, a wire joint is used to “cap” or terminate a wire run. This is done when a given wire needs to end without directly connecting it to another part of the electrical circuit.
With a clearer understanding of the differences between splices, step-downs, and wire joints, let’s look at a few examples of where each type would excel.
Where would each of these connectors excel?
Butt Splices
A butt splice would be the ideal solution when connecting two wires of the same size together. So, for example, if you needed to connect two 12 AWG wires together a butt splice is perfect. They can be used in new installations, during maintenance, when replacing wires, or out in the field for emergency repairs. They are available in heat shrink insulation, nylon insulation, vinyl insulation, and non-insulated. You will commonly find butt splices in 22-18 AWG, 16-14 AWG, 12-10 AWG, or 8 AWG sizes.
Step-downs
Step-downs are useful when you need to connect three or more wires together or when you need to connect wires of various sizes together. They carry a colored stripe on the body of the connector to indicate which side is made to handle specific size wires. A step down may carry a blue, red, or yellow stripe on one side with another color stripe on the other. This indicates which wires the opening is sized for. Red indicates 22-18 AWG, blue indicates 16-14 AWG, and yellow indicates 12-10 AWG. For example, a blue stripe would be able to hold three or more 22-18 AWG wires.
Wire Joints
A wire joint could be used in applications where two or more wires need to be connected. However, they are often employed when a wire or wires end at a dead end. A wire may have a dead end for a variety of reasons such as something as the intended equipment isn’t ready to install but you want the wire ready. If you leave the wire exposed, you run the risk of an electrical short or operator injury. A wire joint allows you to safely close off the wire until you are ready for the next step.
What heat tools should I use with these connectors?
Heat shrink terminals such as butt splices, step downs, and wire joints require the proper amount of heat to be correctly activated. Using a tool such as our
3-temp heat gun is a surefire way to get the temperature that you need. With three settings, this tool quickly reaches 1200°F/648°C. This industrial-grade tool is known for it's rapid heating and long-term durability. Heat guns are commonly used in repair shops marinas, on production lines, and even in private garages.
You can properly operate a heat gun by keeping it a safe distance from what you are heating and continually moving it back and forth in a consistent motion. This quick video shows how to properly activate heat shrink, but more importantly for us, it covers the proper usage of a heat gun.
What crimpers work with these connectors?
To properly install any of these connectors, the correct crimping tool is a must. Two wire crimping tools we would recommend are the controlled ratchet crimper for heat shrink terminals and the ratchet-controlled crimp tool by 3M. The first tool allows you to crimp any heat shrink terminal from 22 AWG all the way to 8 AWG making it handle the wider range of sizes out of the two tools. The second tool handles 22-10 AWG and works with insulated as well as non-insulated connectors. Both tools have been tried and tested on our own production lines, proving their durability and quality.
What resistances or advantages do these connectors offer?
All of the splices, step-downs, and wire joints we have discussed are made from tinned copper. This is done to resist corrosion in the harshest marine conditions and helps to make them resistant to other environmental hazards. Additionally, these connectors are built around the idea of long-term protection and field serviceability. This means that they are easy to install and built to last.
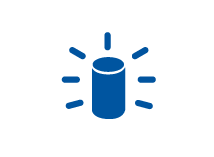
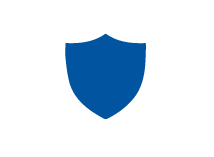
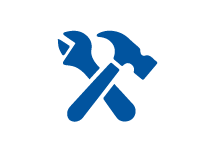
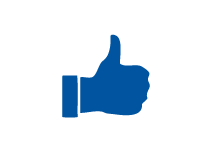
To make our connectors even more effective, they are resistant to several important environmental hazards. These hazards include moisture, impact, abrasion, and chemical exposure. All four of these hazards are common to the marine environment meaning that these splices, step-downs, and wire joints are the perfect choice for marine usage.
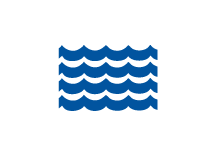
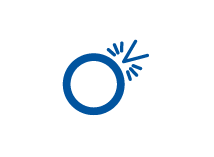
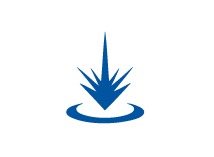
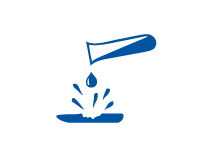