Categories
- Wire & Cable
- Multi-conductor & Signal Cable
- Battery Cable Assemblies
- Terminals and Connectors
- Electrical Parts
- Electrical Tools
- ID Products
- Wire Management
- Tape & Sealant
- Mounting Panels & Panel Blanks
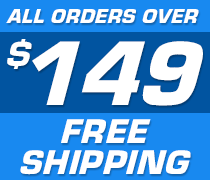
Need Help?
Click HereGet a Business Account
Apply HereFork Terminals
What are fork terminals?
Fork Terminals refer to types of crimp connectors that are used to attach a wire or wires to a stud, bus bar, or another part of an electrical system. A fork terminal is commonly used to help prevent frayed wires and offer a high level of protection. Often times in an electrical environment, vibration is a serious factor. It can cause terminals to come loose and the result is a loss in electrical conductivity. Pacer's has solved this problem by utilizing two unique and distinct solutions; flanged fork terminals and locking fork terminals. Fork terminals offer a secure and safe connection method. These electrical connector types are built for long-term applications. Pacer products are proven industry standard. Don't let a few cents cost you a day with loved ones on the water. Make sure you get the highest quality parts possible.
"Pacer products are proven industry standard. Don't let a few cents cost you a day with loved ones on the water. Make sure you get the highest quality parts possible."
How do you use fork terminals?
Properly using fork terminals is easier than you may think. Let's cover how to use crimp connectors such as fork terminals with a common bus bar. The first step is gathering the parts and tools you will need. We'll be using 14 gauge wire, fork terminals, a bus bar, a stripping tool, a crimping tool, and a heat tool. The first step is stripping the wires to the proper length. Pay careful attention not to damage the insulation or conductors when stripping. With your wires prepped, line up the terminal into the proper crimp nest. Make sure that your electrical connectors are the highest quality possible. The quality of the various electrical connector types will impact your electrical connections. You'll notice the colored dots on the crimping tool indicate the nest by gauge. Next, you'll insert your wire into the fork terminal body making sure that the insulation butts up to the inner barrel. Now simply complete one full ratchet cycle. Once the crimp cycle is complete, you'll want to perform a tug test. Gently pull from both sides of the connection point to ensure that the connection is solid. With your terminals properly installed, it's time to activate the heat shrink with our heat tool. Epoxy-lined heat shrink should be used in marine environments to create an environmentally sealed connection. Now it's time to install our fork terminals on our busbar. Simply loosen the screws you intend to use. Now take your locking fork and press it into the screw. You will want to apply enough pressure to the fork terminal to allow it to firmly hug the screw body. With the fork terminal in place, you can tighten the screw. With a gentle tug, you can see just how durable this connection is. Notice that the fork terminal does not move. Now we just need to repeat the process with the remaining terminals. And that's it. We have successfully installed our fork terminals on the busbar. Fork terminals are extremely useful in electrical connections. They are available in 22-18 gauge, 16-14 gauge, and 12-10 gauge sizes. They are also available in bare, nylon, vinyl, or heat shrink insulation. Fork terminals are an obvious choice. They offer durability, versatility, and longevity even in the toughest environments.
Where are fork terminals implemented?
Fork terminals offer advantages other terminals do not
A fork terminal can be utilized in applications where accessibility and future alterations are important considerations. When used with bus bars, they allow the user to make changes without having to disassemble the entire connection. They are ideal for use in new wire installations as well as replacement parts. If you have faded terminals, damaged terminals, or cracked terminals, then these may just be the terminals that you are looking for. All you will need are the proper tools and some heat shrink depending on the application.
What is the difference between a flanged fork terminal and a locking fork terminal?
Flanged fork terminals and locking fork terminals share some similarities however they are quite different. A flanged fork terminal has the ends of the forks turned up. This action causes the fork terminal to grip the screw or mount that it is attached to. This, in turn, creates a stronger connection and reduces the risk of the terminal coming loose. A locking fork terminal on the other hand has projections inside the fork body. These projections cause the terminal to snap onto the screw. This snapping action again creates a stronger bond and reduces the risk of the connection coming loose. So, the difference is quite clear even if the end result is largely the same. Both of these designs will keep the terminal fastened even if the holding screw loosens.
Flanged Fork Terminal
Locking Fork Terminal
Why use a fork terminal, what benefits does it offer?
A fork terminal can offer a host of benefits that make it a solid choice. A fork terminal offers longevity over other terminals as well as durability. Each Fork terminal is also versatile in its use as it can be used in applications that other types of terminals and connectors cannot be used. The fact is that a standard terminal can potentially disconnect should the holding screw loosen over time. With Pacer fork terminals you ensure the longevity of your connection and the conductivity of your electrical system.
Durability
Versatile
Longevity
What is the difference between a fork terminal and a ring terminal?
The main difference between a fork terminal and a ring terminal is the way in which each is used to connect to an electrical system. A fork terminal can quickly and easily be attached to a stud or screw without having to fully remove the screw or nut. This fact alone can save time in the long run, especially on larger jobs. With a ring terminal, you would need to fully remove the screw or nut in order to properly apply the terminal. The bottom line is that both fork terminals and ring terminals have the applications that they are best suited for. The trick is knowing when to use each.
A Ring Terminal
A Fork Terminal
What tools should I use with a fork terminal?
A fork terminal can only be used with the proper type of crimper which will give the strongest connection possible. This ensures the proper pressure and a long lasting connection. The most versatile crimper we offer is the VTTR50 which can crimp any fork terminal available other than the non-insulated types. If you need to crimp non-insulated terminals for your application, use our VT3120CT which can work with every fork terminal available. Make sure that you have the correct tool to handle your crimp connectors or electrical wire connectors. Both of these tools work exceptionally well with a fork terminal. We use both of these tools on our production lines which just goes to show how much trust we put into these tools. If we trust them enough to use them on our products, you can trust them as well.
What types of fork terminals are available?
Pacer carries fork terminal wire connectors in 22-18 AWG, 16-14 AWG, and 12-10 AWG in both flanged and locking styles. This means that you can get 12-10 AWG locking fork terminals or 22-18 flanged fork terminals. We offer many of our fork terminals in heat shrink, nylon, vinyl, and non-insulated body styles. In this way, we ensure that you can get the exact type of fork terminal that you are looking for. One question that we frequently receive is how important the insulation type is.
12AWG-10AWG
16AWG-14AWG
22AWG-18AWG
Does the insulation type really matter?
Insulation plays a crucial role in the life and conductivity of an electrical connection. Using the wrong type of insulation for a given application can result in undesired outcomes. We carry heat shrink to give the highest level of protection possible. With a heat shrink fork terminal, you can create an environmental seal that can outlast other insulation types. Nylon insulation is the next step that offers strong protection but not environmental protection. Vinyl is cost-effective but offers less protection than nylon. Non-insulated is the most affordable option but you compromise some of the protection you get with the other types of insulation. It all boils down to what your specific application requires.
Heat Shrink
Nylon
Vinyl
Non-insulated
Why choose Pacer?
Pacer has served the marine and wire industries for over forty years and has used that time to build a reputation as an industry leader and a trusted source. We are continually chosen by some of the world’s largest boat builders for their electrical needs. We are also the frequent choice of local and national repair shops, marinas, and private boaters. Pacer products are a proven industry standard. We only stock the highest quality parts for our partners. Throughout our time in the marine and wire industries, we have had a long-term focus on quality and customer satisfaction. When you order from Pacer, you know that you are getting quality.
*This page was updated on 2/07/2023*